Line for the production extruded combi-feed of up to 150 kg / h “Waiz-150”
The line is intended for the production of extruded combi-feed for poultry, fish, cattle, pigs, horses.
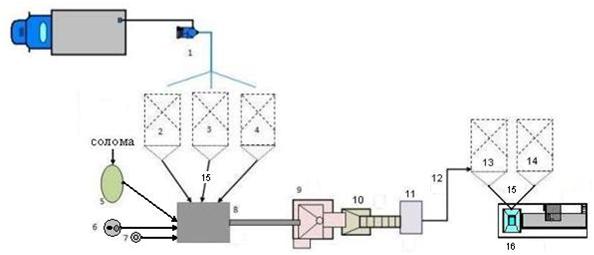
The use of extruded feed:
-provides digestion and stimulates the digestive tract of young animals;
-improves the safety of young livestock up to 95%;
-increases thequantity of received milk up to 20%;
-increases the average daily weight gain up to 20%;
-reduces feed consumption by ~ 20%;
-increase the feed digestibility up to 90-95%;
-increases feedshelf life up to 6 months enables usage of substandard grain;
-improves the energy value of combi-feeds.
-provides digestion and stimulates the digestive tract of young animals;
-improves the safety of young livestock up to 95%;
-increases thequantity of received milk up to 20%;
-increases the average daily weight gain up to 20%;
-reduces feed consumption by ~ 20%;
-increase the feed digestibility up to 90-95%;
-increases feedshelf life up to 6 months enables usage of substandard grain;
-improves the energy value of combi-feeds.
The line consists of:
1 - Grain pneumatic conveyor (optional);
2 - hopper with wheat (black metal, 8 m3 - 6 tons of grain);
3 – hopper with corn (black metal, 8 m3 - 6 tons of grain);
4 – hopper with oats (black metal, 8 m3 - 6 tons of grain);
5 - straw crusher-grinder (optional);
6 – tunk for bulk additives - (optional);
7 – tunk for liquid additives - (optional);
8 - mixer with a screw conveyor;
9 - feed extruder;
10 - conveyor (optional);
11 - crusher;
12 - air conveyor (optional);
13 - storage bin (black metal, 5 m3);
14 - storage bin (black metal, 5 m3);
15 - screw conveyor (option 6 pcs.);
16 - packaging apparatus for filling bags of 25 kg (optional);
17 - remote-automated line control unit (optional);
2 - hopper with wheat (black metal, 8 m3 - 6 tons of grain);
3 – hopper with corn (black metal, 8 m3 - 6 tons of grain);
4 – hopper with oats (black metal, 8 m3 - 6 tons of grain);
5 - straw crusher-grinder (optional);
6 – tunk for bulk additives - (optional);
7 – tunk for liquid additives - (optional);
8 - mixer with a screw conveyor;
9 - feed extruder;
10 - conveyor (optional);
11 - crusher;
12 - air conveyor (optional);
13 - storage bin (black metal, 5 m3);
14 - storage bin (black metal, 5 m3);
15 - screw conveyor (option 6 pcs.);
16 - packaging apparatus for filling bags of 25 kg (optional);
17 - remote-automated line control unit (optional);
Brief description of extruded combi-feed production
The initial grain components is loaded from car or another vehicle into the storage hopper (2, 3 and 4)using a mobile air conveyor (1) (option) (pneumatic loader) or manually. Pneumatic loader (optional) is a mobile unit with a fast-mounted pipelines. According to the given feed receipt, the grain forage is fed into the mixer (8) mounted on the weight sensors, fixing and controlling the incoming dose of ingredient, using bins screw conveyor (option) or manually.
Depending upon the feed formulation, the straw, dried grass and so on may be used as an ingredient. In this case, for example, baled straw is loaded manually into crusher - grinder (5) (optional). The work of this unit controls the control unit on the mixer by turning on and off the crushing process (at a given parameter of weight for one batch) and feeding grinded component into the mixer.
The system for making food supplements, additives and premixes (optional) is also provided. For this, the additives are fed from the hopper of dry additives (6) into the mixer by strictly predetermined quantity, via the screw conveyor (optional) or manually. It is possible to use liquid premixes. In this case, it is better to use a container for liquid additives (7) (optional).
It is also provided the synchronous introduction of these additives. The dose of premixes is measured strictly by the mixer. On the automated control unit, it should be set a program that eliminates the start of mixing ingredients until it is made a predetermined amount of weight for each component that allows to exclude non-compliance with recipe.
When all ingredients achieved set weight parameters in mixer (according to formulation, given to the control unit), it starts mixing process.
The mixer tank capacity makes 210 дм3. The weight of one batch is adjusted from 50 to 120 kg. The mixing time is 5 - 10 minutes. At line productivity of 150 kg / h, the optimum batch weight is 50 and 75 kg, which is respectively 3, and 2 cycles per an hour.
After completion of the mixing process, the raw material enters to the hopper of an extruder (9)via a screw conveyor (optional) or manually. Upon completion of unloading, the mixer starts a new cycle of loading and mixing. Meanwhile, the product is dispensed from the hopper into the extruder.
The extruder operates continuously, as it is happening timely additional loading of raw materials from the mixer into a hopper of the extruder by filling control device that eliminates the utter devastation of the hopper during operation of the extruder. Also, this controller stops the loading in case of filling hopper level. The mixer performance exceeds the performance of the extruder, which also contributes to the continuous operation of line.
During extrusion of grains it is considered a short-time temperature and pressure impact resulting in the converting of structure and properties of nutrients. We can receive a structured feed having high taste and nutritional properties. During the short period of time all compounds are simultaneously mixed, pressed, grinded, heated, boiled, sterilized and formed. A sharp pressure drop during the product exists from extruder trunk, which leads to the deep conversions: the walls of cells and chemical compounds brake, raw material structure changes, microflora (bacteria, fungi) is destroyed. Extrusion treatment increases the product digestibility due to its conversion into easily digested form of the raw material components both animal and plant origin and complete disinfection of food.
The extruded product is fed to a crushing mill (11)through the conveyor (10) (optional) or manually. The crushed extruded product is loaded into the storage hopper (13 and 14) by pneumatic conveyor (12) (option) or manually.
The final stage of the production line is the packaging of the product (optional). From the storage hopper the product via the screw conveyor (15) (optional) or manually enters into the semi-automatic filling unit (16) (optional), equipped with a batcher, conveyor and package sewing machine. The weight of dose is adjusted, the maximum weight - 25 kg.
The whole operation process of line depending on the combi-feed formulation, is controlled by the programmable remote-control unit (optional).
Technical specifications:
Power supply(all devices) - 380 V, 50 Hz;
Power consumption of line: 48kW;
Area: 80m2;
Servicing personnel – 2-4employees.
Warranty on equipment - 12 month from commissioning;
Delivery time – 90 days.